Design for Injection Moulding
The biggest factor in Injection Moulded part quality comes from the part design. It's the cheapest point at which to make improvements, so lets have a look at how to produce consistent parts that save you money...
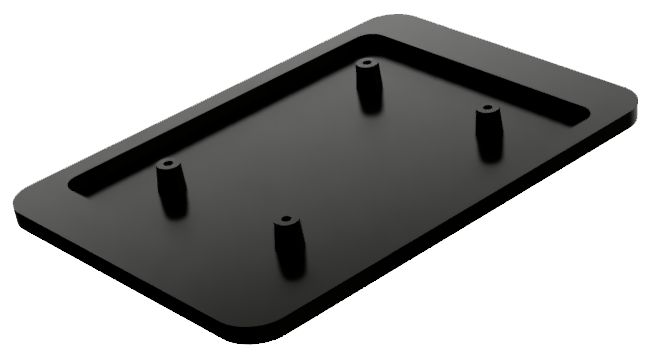

The Basics
Overview of Injection Moulding.Injection moulding is a process that allows a plastic part to be reproduced by forming molten plastic in a metal mould.
The mould is a metal structure which has a hollow inside of it in the form of the part to be moulded. We call this hollow the cavity.
Small platic pellets are loaded into a hopper which feeds a heated barrel. In the barrel the pellets are melted and fed towards the mould. In basic operation the mould closes, the molten plastic is forced into the mould under considerable pressure, then it is held closed until the plastic has solidified. Once the plastic is formed the mould opens to allow the part to fall out of the machine, and then the process repeats.
Design for Manufacture from the Start
Improve part quality whilst reducing tool and part cost.No-one wants to redesign a part from scratch because it doesn’t meet the requirements for manufacture. The solution is to understand the manufacturing process from the beginning of the part design, and contact the manufacturer to ask guidance when required.
The first step is to understand if Injection Moulding is the correct process for your part. It is a process that leads to low unit cost, high repeatability and tens of thousands to millions of parts from a single tool. Where the process is not suitable is for objects such as bottles with a void that is geometrically impossible. It is not a process suitable for creating a part and then making amendments after the tool has been completed, as this is costly and time consuming.
The first step in the design is to look at your part and decide where a split line is likely to be. This will decide how and where to apply draft to the part.
When designing ensure that each time you extrude or cut a feature you add in a suitable draft angle to allow the part to come out of the tool. More on this in later steps. You can have undercuts and flat sides but these may come at additional cost. Consider using in-built draft analysis tools as you progress through the design to identify problematic surfaces.
The key cost component to a tool is the inclusion of any undercuts that have to be addressed with the use of collapsible cores, side moving elements and lifters. Where possible try to rethink your design to exclude these and also consider that 2 parts with no undercuts may be cheaper than 1 complex part with them.
Finally listen to the advice of your manufacturer who wil have a vested interest in making your parts easy to manufacture to your requirements. Swift Mould will always be happy to guide you in these decisions.
Draft Angles
Ensuring the part ejects from the toolOnce plastic has been injected into the cavity it will cool and shrink. If the par shrinks onto a vertical surface with no draft then the part can require a significant force to remove it from the tool. Not only can this damage the surface of the part but it can lead to stuck parts, reduced production and higher part costs.
Generally speaking for most applications a 1.5 degree draft angle is more than sufficient for successful part production. If you wish to use a rough surface finish then consider increasing this to 3 degrees and otherwise the surface may end up with drag marks.
A common mistake we understandably see is where there is draft but in the wrong direction. Consider using a draft analysis tool common in most good CAD packages to analyse this. We are of course always available to check your part however, so feel free to get in touch with us.
Undercuts
Side Movers, Cores & LiftersThis is a feature of when the tool cavity opens one way, and your part needs a hole or feature in the other direction. Sometimes this is avoidable through clever design features and in other cases it’s completely unavoidable.
Undercuts are one of the biggest factors that affect tooling cost so they are worth considering carefully.
A common mistake when designing these undercut features is to design them all at different angles to the part. Each angle will require a different element and subsequent cost. Try to create as many features so they are in the same draw direction, thereby eliminating the number of mechanical elements required in the tool.
There are times where there is an undercut that can be resolved into a simple open and close feature (a feature that no longer has the undercut). Consider if an undercut can be prevented by coring a hole underneath the undercut itself allowing another part of the tool to reach the feature. This is especially a common practice when practical for items such as clips.
Meet our Clients
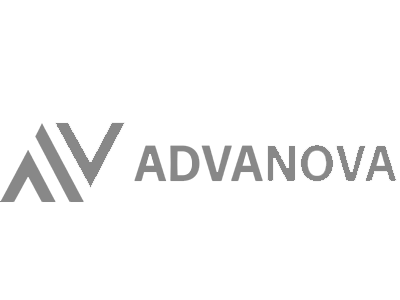
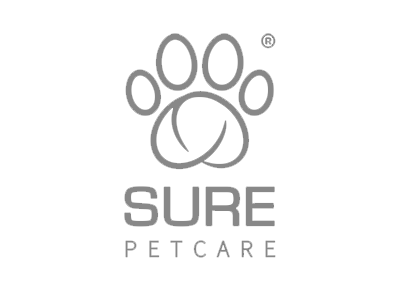
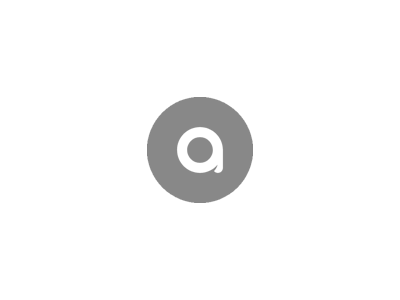
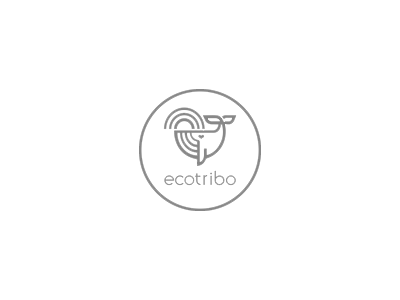
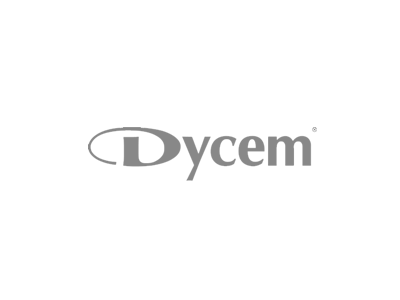